Saint Ann's Sheet Metal Co Ltd
East Midlands based St Ann’s Sheet Metal manufactures a universal range of sheet metal components from sheet metals such as mild steel, stainless steel, aluminium, galvanised steel, Zintec and plated metals.
As an ISO 9002 accredited company, our commitment to superior workmanship and excellence has earned us a reputation for producing high quality, competitively priced sheet metal components that give our customers a distinct advantage.
Saint Ann's Sheet Metal Co Ltd Overview
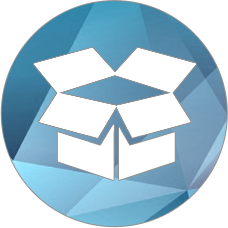
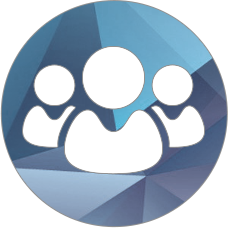
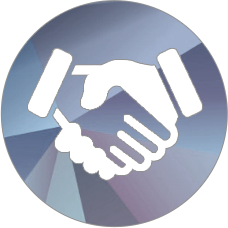