Proctor Process Plant Ltd
Proctor Process Plant specialises in the application of industrial gas burners and combustion equipment to process industries, operating in a wide variety of market sectors both in the UK and Overseas.
Product Range Includes:
- Industrial Gas Burner
- Package Burners
- Induct Burners
- Bar/Singe Burners
- Tube Firing Burners
- In-direct Systems and Heat Exchangers
- Oil Fired Burners
- Infra-Red Heating Solutions
- Instrumentation and Control Systems
- Fuel Conversions
- Industrial Gas Pipework Design, installation and Certification
- Automotive
- Chemical
- Food Industry
- Injection and Rotary Mouldings
- Surface Coatings
- Textiles
- Underlay
- Web Treatment
Proctor Process Plant Ltd Overview
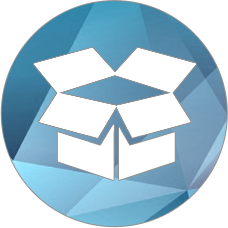
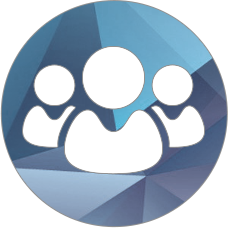
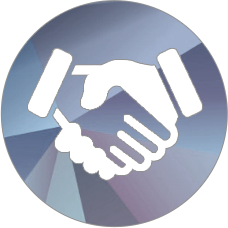