Venturi Jet Pumps
Liquid Jet Eductors use the kinetic energy of a liquid to entrain another liquid. They completely mix the two, then discharge the mixture against a counter pressure. They are used in large numbers throughout industry for pumping and mixing operations.
Applications are so vast, it is impossible to note all of them.
General uses include:
- lifting
- pumping
- mixing and agitating of liquids
- handling granular solids and slurries
Some of the typical applications can be seen below:
- Draining flooded cellars, Emptying tanks and sumps or bunds, Pumping and mixing operations in oil treating systems
- De-watering sand and coal barges, Introducing anti-knock fluids and colouring matter into gasoline
- Continuous blending, Acidifying, Causticizing of oils, Mixing drilling mud, Producing emulsions
- Pumping food products, Pumping sand and filter clay or activated carbon
- Tank mixing, and various Proportioning operations
Venturi Jet Pumps Overview
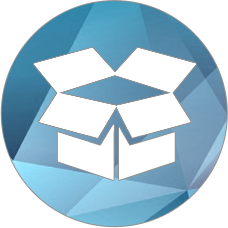
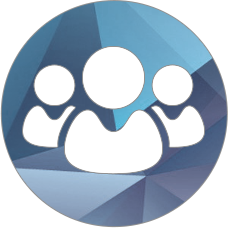
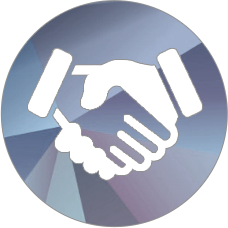