Airprotekt Ltd.
AirProtekt’s focus is on providing tailored Air Pollution Control solutions by using key technologies to deliver guaranteed emissions. Established in 1994, AirProtekt was created from the former Environmental Products business of Johnson Matthey plc. Honeycat Catalytic oxidation systems worldwide, Airprotekt's PMC catalysts have been installed in thousands of catalytic oxidation systems.
The Platinum Group Metal catalysts, which form the heart of a Honeycat catalytic oxidation system, are derived from well-proven autocatalyst technology and offer numerous benefits compared with rival catalytic systems.
Flowrates that can be treated in a single catalytic oxidiser range from 10m3/hr to 60,000m3/hr;
Catalyst modules for installation into existing process exhausts, utilising only the process temperature and pressure (eg ovens, kilns and out-of-compliance thermal oxidisers);
Â
Airprotekt Ltd. Overview
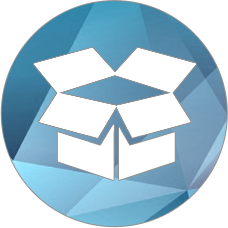
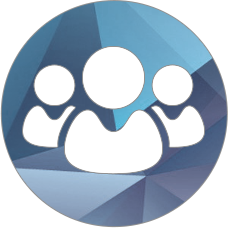
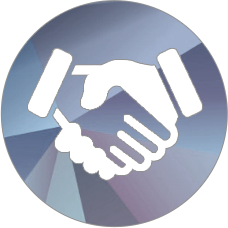