Andel Plastics Ltd
Andel Plastics Limited is one of the UK's leading injection mould toolmakers and plastic injection moulding providers to the whole of the UK. In our 40th year we have seen the completion of a Class 7 cleanroom. Making Andel Plastics Ltd one of a very few companies who have a toolroom, injection moulding facility and Class 7 Cleanroom all under one roof. Already holding the ISO9001 Quality Certification and ISO13485 Medical Quality Standard. You can be assured of a full manufacturing facility for a wide range of industries, including Medical device manufacture and packaging, Signalling, Plumbing, household products etc.
Based in Tyseley, Birmingham Andel has been Intelligently engineering solutions to its customers since 1975. Our approach is always to provide engineering excellence in both component design, tool design, precision mould tool manufacture and quality injection mouldings. Andel Plastics can offer post moulding works such as bespoke packaging or assembly to reduce the number of post operations.
We have been at the forefront of developing metal replacement plastic parts without compromising on the end products effectiveness or quality.
View, save, and or print our brochure. Requires Adobe Reader available at get.adobe.com/reader.
Injection Mould Toolmakers
Andel Plastics Ltd has a fully equipped in house toolroom for the design, manufacture and repair of injection mould tooling.
We pride ourselves on making the best quality precision injection mould tools within the UK. We are so confident in the quality of our tooling that we provide a 10 year maintenance free guarantee on all production injection mould tooling that we manufacture and mould in-house.
We have invested in a standard bolster set, which means that we can potentially reduce tooling costs for our customers by using this standard set. Thus only needing to manufacture the cavity inserts for a customers part.
Due to customer demand we now offer aluminium tooling and inserts. This not only allows us to reduce lead-times, but means we can manufacture the prototype tooling four our customers cost effectively, then take an lessons learnt during this development process into production tooling.
Having recently invested over £200K in the toolroom equipment, we also have two new trainee toolmakers learning the craft of the Andel way of manufacturing tooling. This way protecting the future quality through our expansion remains constant.
At Andel Plastics intelligent engineering is our competitive edge, demonstrating engineering excellence through the solutions that we achieve for plastic products. One of our specialities is Overmoulding and insert moulding plastic to metal, manufacturing parts for the automotive, signalling and plumbing industry. Another leading industry example of our intelligently engineered component solutions revolves around the trend for metal replacement plastic products. Being able to offer our design and vast experience in the this area to convert a product that is currently made out of metal to plastic without compromising on the robustness or quality of the original metal product.
Injection Mouldings
At our Tyseley based factory, Andel Plastics has a fully equipped injection moulding plant ranging from 20 to 200 tonne machines. With over 40 years experience in the processing of polymers, we have an enviable knowledge of utilising them in plastic component manufacture.
Andel has worked for many years in the area of overmoulding and insert moulding metal parts with the plastic to give a more robust component without the need for post assembly, gluing or hot staking.
Our approach to injection moulding means we are happy to offer small batch moulding services as well and full production runs. We range from batch sizes of 100 parts to 110,000 parts without issue.
One of the benefits of having an inhouse toolroom is the ability to prove out a tool without having to keep moving between moulder and toolmaker. Likewise there is less down time in routine maintenance and repairs when the moulder and toolmaker are under the same roof.
Class 7 Cleanroom West Midlands
Andel Plastics' 40th year in business saw the installation of a Class 7 Cleanroom into its Tyseley premises in Birmingham. With aide from the Business Innovation Funding from Birmingham City Council the cleanroom project was completed by Airology within 6 weeks.
The inclusion of a cleanroom at Andel Plastics now means we can offer a full manufacturing service for medical devices, with the added confidence of both ISO9001 and ISO13485 Quality Standards.
An upcoming project will see the injection mould tools designed and manufactured in our inhouse toolroom. Plastic components being injection moulded within our Birmingham premises, then these being moved into the Class 7 Cleanroom for inspection, assembly and packaging before being shipped for sterilisation. This now means that our customer, who was going to have to use three separate companies to achieve this can now just come to Andel Plastic for the full medical device manufacturing and packaging service. If you have any cleanroom requirements please do not hesitate to contact us.
Markets for our mouldings
At Andel Plastics we aim to keep our markets broad and without exclusion. Currently we are spread across a wide range of industries which gives us a good basis for a wide range of material selection that is correct for the component usage. We manufacture many parts for Signalling, Plumbing, Automotive markets etc.
One of our growing markets is the Medical market, whilst we have been moulding plastic medical components for many years we have installed a Class 7 Cleanroom to enable us to further our capabilities in the medical and healthcare industry. This is now working and accredited with the ISO13485 Medical Device Quality Standard assuring of the best service in all areas with one management team.
Medical Device Manufacture
The recent installation of a Class 7 Cleanroom at Andel Plastics, means we can now offer a full manufacturing service for medical devices. With our design service we can help design medical device components for manufacture using the injection moulding process, as well as suggesting added value options like overmoulding if appropriate. Our inhouse toolmaking manufacturing centre can then make the mould tool to produce the plastic components needed for the device. We can then transfer product to the cleanroom for inspection, assembly and packaging. This is a new addition to our services at Andel and we are looking forward to seeing where it can take us. Currently we are packing single use surgical procedure packs for a wide range of small procedures. We also injection mould and assemble a testing device within the cleanroom. Our accreditation to the ISO13485 Medical Device Quality Standard provides the reassurance that all our products are handled and manufactured with full traceability. The possibilities are endless, if you think we can help you with the design and manufacture of your medical device, please do not hesitate to contact us.
Mouldflow Analysis
Andel utilises the Visiflow software system to carry out Mouldflow analysis on our components prior to finalising tooling design.
Offered as part of the toolmaking service this enables us to design out as many potential issues as possible in turns of weld line areas, gas traps and feed points.
Whilst we carry out this service as part of our usual customer service process, we can offer this as on a subcontract basis.
Assembly Jigs and Fixtures
As part of our services at Andel we are able to offer post operative work on plastic components. We regularly manufacture parts that need assembling into the finished product and packaging into our customers branded packaging. This means that the customer can receive a complete product without requiring to ship components from one place to another for assembly. To this end we provide a machining and assembly service and can manufacture the bespoke jigs and fixtures to make this happen.
We also offer ultrasonic welding in-house, 2019 will see the addition of a two colour printing service, to further our services to customers.
Component Design
When designing a component it is important to consider the feasibility of manufacture. We often find customer arriving with a CAD model that may give them a plastic component that they want, but has been designed in such a way that the tooling costs are astromically high or indeed cannot be done in an effective way that still gives a quality finished component. It is for this reason that we urge product designers to contact us to discuss the requirements of the component and let us help them design the part for manufacture.
People are often surprised how the removal of an undercut or coring out can improve the asthetics and cost of the tooling and the individual plastic moulded component.
It is our aim to try and talk to designers at the start of the project to advise them what is and is not possible and moreover what can be improved at the earliest stage in design and development of a part. Which is why many of our longstanding customers arrive with little more than a sketch or a plasticine model of what they are thinking about. Andel uses Visiflow, to be able to offer an in-house mouldflow analysis service. We utilise this as part of our routine project management service, but are also able to offer this on a subcontract basis.
We can also advise on material choice for the products environment, which has impacts on the product design to achieve a nicely finished product without sinks and flow lines. Please contact us to discuss your requirements.
Contact Us
" For Further Information CLICK HERE"
Andel Plastics Ltd Overview
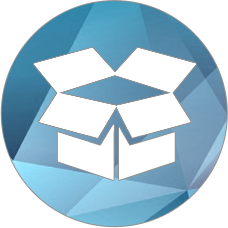
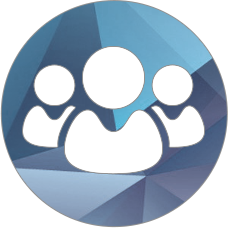
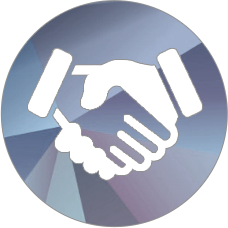