BEP Surface Technologies Ltd
BEP Surface Technologies Ltd was founded in 2004 with the amalgamation of the Bury Electroplating Company and BEP Grinding Ltd. Based in Radcliffe at their expansive premises the company are able to provide a high quality service to customers. The company has clients in a wide variety of industries and continues to serve them with the commitment to quality and service that the companies are renowned for:
- Acid Cleaning
- De-Gassing
- Hard Chrome Plating
- Nickel Plating
- Copper Plating
- Copper Shelled Rolls for the Plastics Industry
- Ultra Finish
- Ultramat Textured Finishes
- Turning & Precision Cylindrical Grinding
For technical help and advice please contact our technical team on 0161-724 9090
BEP Surface Technologies Ltd Overview
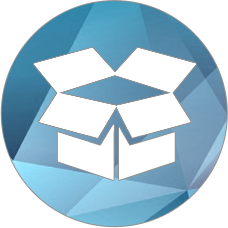
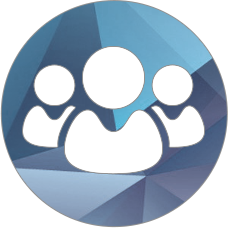
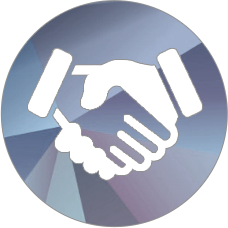