C Perkin Ltd
Manufacturers of paper tube and cardboard core making, cutting and finishing machinery.
- Core Winders
- Knife Units
- Composite Can Labellers
- Slitters
- Rewinders
C Perkin Ltd Overview
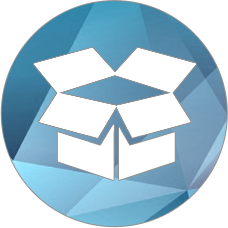
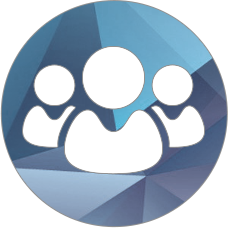
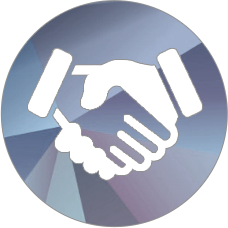