E Magnets UK
Magnets are in Our Blood
We specialise is the design and supply of a wide range of Permanent Magnets, Magnetic Assemblies, Factory Magnet Solutions, and Magnetic Products. Included in our Magnet Product Portfolio are the Neodymium Rare Earth Magnets (NdFeB - the strongest permanent magnets in the world), Samarium Cobalt Rare Earth Magnets (SmCo - strong permanent magnets that maintain strength at high temperatures), and standard strength Ferrite Magnets.
E Magnets UK Overview
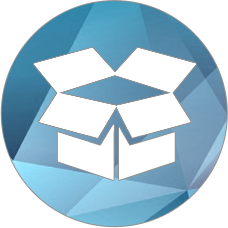
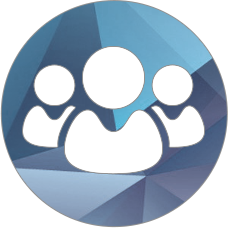
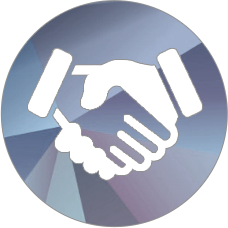