Firma-Chrome Ltd
In the current UK climate engineering is becoming more specialised. To service this need a high degree of expertise is required to complement the products and services that will survive. Demands on corrosion protection, wear and aesthetics, coupled with the ever present pressure to reduce the environmental impact require specialists in each field.
Firma-Loy is such a specialist. Our aim is to make available all the best techniques, the most responsive service on one site where the environmental impact will be contained & eliminated where possible.The processes detailed in the following pages can only give a flavour of our range and versatility so please contact us if you have other requirements.
Firma-Chrome Ltd Overview
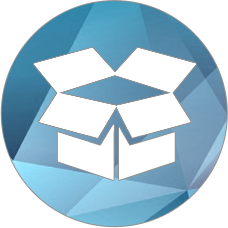
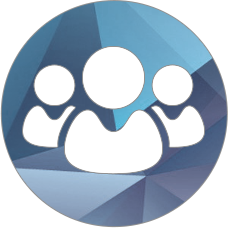
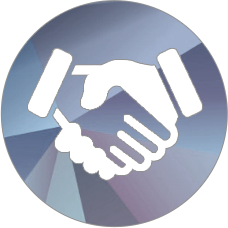