GMS Ball Company
Welcome to GMS Ball Co Ltd
We are an independent suppler of all types of steel balls - and balls in many other materials, in quantities ranging from tens to millions.
We deal with ball manufacturers in all parts of the world and our purchasing volumes allow us to negotiate extremely competitive pricing.
How can GMS help you
If you already buy steel balls you will know that over the last few years a significant proportion of ball production has moved from Europe and the USA to India and the Far East. Some of these sources are very reliable others are not.
GMS deals with many of the more reliable of these manufactures, but we fully inspect all of the balls we buy. In this way we can offer you a reliable European source of steel balls, guaranteed to meet your specification every time.
GMS Ball Company Overview
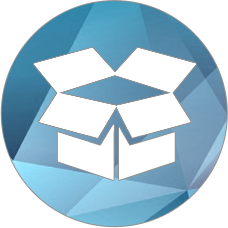
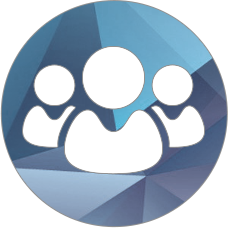
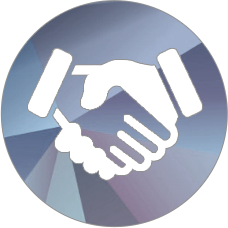