HV Wooding Ltd
HV Wooding are specialists in the manufacture of metal components offering a component and assembly service to industry in the following areas:
Industries serviced include:
- Presswork - 5 - 140 tons.
- Tooling - Sub-Contract Service.
- Copper Busbars, Aluminium Busbars, Cuponal Busbars
- CNC Punching, Forming
- Tin & Silver Plating.
- CNC Wire Erosion - Aerospace, Medical & Motor Sport.
Industries serviced include:
- Switchgear/Control Panel/Panel Boards
- Transformers
- Marine
- Rail
- Automotive
- Electronic
- Electrical
- Medical
- Aerospace
HV Wooding Ltd Overview
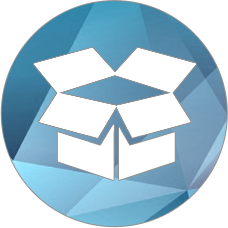
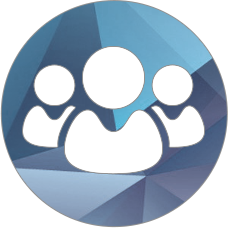
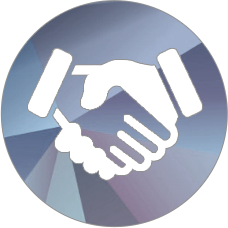