Prima Electronic Services Ltd
As a contract electronics manufacturer based near Cambridge UK, Prima Group brings to the East Anglia region over 22 years of electronic manufacturing experience. Offering a wide range of electronic manufacturing services, including printed circuit board assembly (PCB assembly), surface mount assembly, and conventional electronics assembly, Prima specialises in electronic manufacturing development from prototype, through NPI and full production of medium size batches (20 - 400) of complex and non-complex electronics products.
Automated Storage and Kitting
The benefits associated with automated storage include:
- All parts issued on a FIFO basis.
- All parts stored & retrieved under automated control
- All parts bar-coded when loaded into the system thereby increases control of storage and retrieval
- Pick lists bar-coded to reduce picking errors
Fine Pitch Solder Pasting
One of the cornerstones of reliable board building is ensuring that when the solder paste is applied to the pads on the board that exactly the correct amount of paste is put down, and in the right place.
The Fuji fine pitch printer will accurately position the stencil and the board together with an optically calibrated and adjusted movement to ensure that they are accurately aligned within microns.
These machines will place parts on pads down to 300 micron pitch between pads.
Surface Mount Assembly
Prima has a policy of constantly renewing its investment in equipment in order to be able to offer the best solution to the growing changes in surface mount technologies.
The current list of placement equipment used is as follows:
- Yamaha iPulse M1 Placement machine
- Yamaha iPulse M4 Placement machine
- Yamaha iPulse M4 Placement machine
- Yamaha iPulse M4 Placement machine
- Yamaha FV7100 Placement machine
Vapour Phase
Recognising that conventional reflow techniques are not always the best to use for lead free boards Prima has invested in Vapour Phase soldering.
The technique of immersing the board in the vapour allows the vapour at higher temperatures to penetrate every nook and cranny of a solder joint and give an even temperature distribution in and around the solder joint at the moment of reflow of the solder paste. Because this happens in an inert atmosphere, this provides a more consistent and reliable solder joint.
Control of Reflow
With forced air reflow soldering it is important to have consistent temperature control in the heating zones so that correct ramp up and ramp down profiles can be achieved.
The Essemtec reflow oven used by Prima provides all these facilities for both lead free and leaded boards.Automatic Optical Inspection
Over the last 10 years or so Automatic Optical Inspection AOI of both solder joints and component placement has developed and grown to become a tool of real value for manufacturers.
Beset by issues of false failures, or worse, false passes, whilst providing some benefits these machines were treated with a degree of scepticism, and they were very hard to programme.
This is no longer the case.
AOI can be programmed directly from the original CAD files, so that programme generation is a very fast activity. Yields have improved enormously to the extent that the results can now almost always be relied upon with confidence, and solder joints even for lead free joints are reliable.
The machine is therefore used to examine solder joints for visual integrity, skewed or misplaced parts, missing parts, tombstoned parts and other potential process induced problems.
Through Hole Build
We have people who are certified IPC trained trainers, and whose knowledge and skills are passed on to new recruits.
We use Royonic light guided semi automatic placement machines where the batch sizes of through hole products requires consistency of build and each operator is required to accept responsibility for their builds. In this way ownership is taken by the operator and as a result quality of second finish and conventional builds is enhanced.
Flying Probe Test
At some point in the manufacturing process the board needs to be tested to ensure that the elements that make up the board are working to specification, so that when it comes to powering it up there will be a high level of confidence that it will function.
Flying probe testing provides for this. The tester tests for electrical shorts and opens. It also tests the value of the components and their tolerances. If it were possible to test for 100% coverage, and if the design is solid then in theory the board will function as the designer intended without any further test.
X-Ray Inspection
Pre reflow
The problem associated with soldering BGA's to boards have to do with the invisibility of the joint on a ball by ball basis.
The use of X-Ray is one of the tools Prima uses to confirm the integrity of the pasting process.
The grey scale image of an array of balls which shows where the ball is relative to the pads in the solder paste gives a fair indication of the alignment or otherwise of the placement or the registration of the paste on the pads.
Post reflow
The soldering process can in of itself cause registration or alignment issues but also create voids inside the collapsed solder ball. It is important to be able to examine BGA's post reflow to ensure that they have been put down correctly, at least visibly.
Boundary Scan Test
One of the more problematical issues surrounding board building has grown to be the use of higher and higher pin count BGA's.
The problem is that in soldering these to a board there is no obvious way to check to see if a pin (ball) has actually collapsed and made a good connection between the device and the board. Even with a perfect process there may still be issues because of the quality of the device selected. To compound the issue if more than one JTAG enabled device is used on the board and they are connected to each other but through a virtual net then there may be no physical test access to find out if the ball has reflowed correctly.
CONTACT US
Remember to mention Applegate Directory Ltd when you Call.
Prima Electronic Services Ltd Overview
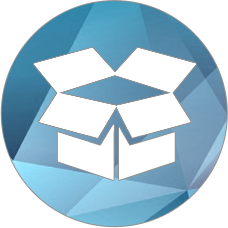
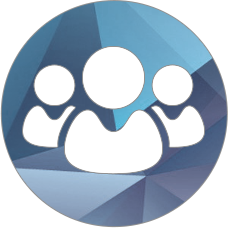
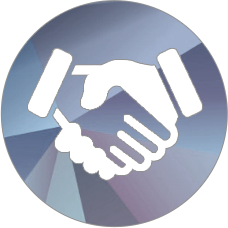