Process Combustion Ltd
Process CombustionĀ Ltd has extensive experience in the design, manufacture and supply of gas and liquid thermal oxidisers, which safely and effectively destroy wastes and off-gases from a diverse range of industries worldwide including waste products from the production and processing of chemicals, food, glass, pharmaceuticals and the motor industry.
Process Combustion Ltd Overview
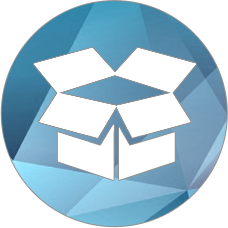
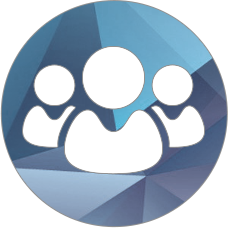
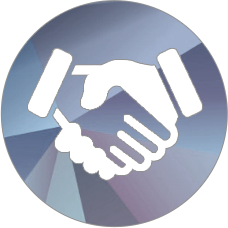