Ricoh UK - Telford
RICOH Rapid Fab 3D Printing Service
RICOH are world leaders in technology and are focused on driving your projects forward by supporting your business’s engineering and additive manufacturing innovations.We’ve created everything you need for a complete Additive Manufacturing service.
At our state-of-the art RICOH Rapid Fab Additive Manufacturing facilities, we combine advanced AM innovation with the highest of quality control standards.
If you have 3D designs that you require printing, we have a range of packages and services making up our complete offering, we can help you choose the right level of service you need to get the most out of our expertise and your ideas.
Ricoh UK - Telford Overview
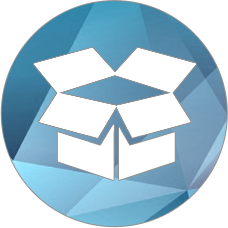
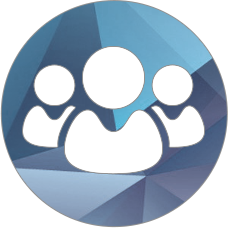
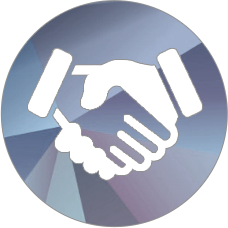