SCHMIDT Technology Ltd
The SCHMIDT® HydroPneumaticPress range consists of a modular system suitable for transforming, joining and assembling optimally within the pressing force range 15 – 220 kN.
With the addition of the SCHMIDT® Press Control 600 and the optional process monitoring, these presses become EC type-approved, CE-conformed workstations. Therefore these press systems can be used in either single cycle mode or automatic mode.
The application determines selection of the press system. Consideration is given to the flexible design of the assembly location taking into account the ergonomic and safety aspects. These characteristics are achieved by means of a finely adjusted, modular type product range. The efficiency and increased process reliability of these press systems have been proven many thousands of times, in single applications, semi-automated assembly systems and have been integrated into automated production lines.
SCHMIDT Technology Ltd Overview
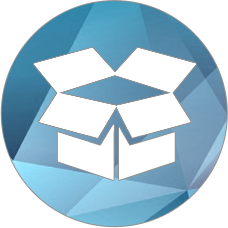
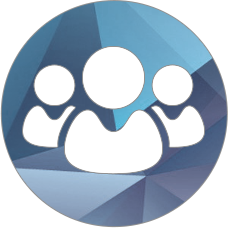
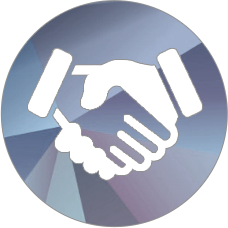