Sprint Electric Ltd
Are you looking to retrofit a DC motor application? Or are you engineering a new control system and looking for a flexible DC motor controller? We can help you choose the best DC drive for your needs.
You can choose from a wide range of variable speed dc drives – from low voltage up to 265Kw. Whether you need single-phase dc drives, three-phase dc drives or a combination of both, we are pleased to provide free pre-sale advice.
Sprint Electric Ltd Overview
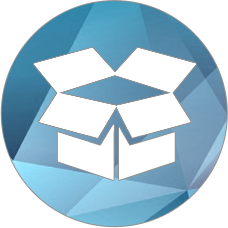
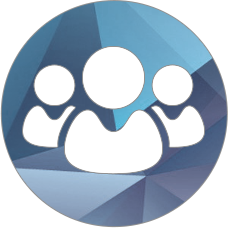
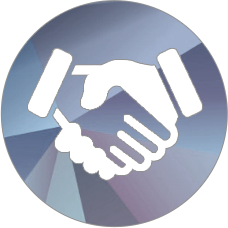