Summit Recycling
Summit Recycling is a division of the multiple award winning; ancillary equipment supplier, Summit Systems. For over 20 years Summit Systems have been supplying ancillary equipment to the plastics industry, including Shredders, Granulators and Material Handling equipment.
Summit Recycling offer waste recycling equipment that ranges from single machines up to large scale post consumer waste operations.
Sourcing from the world's leading recycling technologies, we give customers freedom of choice and confidence in an experienced, dedicated team.
Summit Recycling specialises in the reclaim market, whilst continuing to maintain the exceptional standards of the Summit Group.
- A genuine 24 hour/7 day a week service promise - we were pioneers of this service and we are still the most trusted provider.
- In excess of £2 million spares stockholding here in the UK. Most spares orders placed by 3pm can be delivered the next day.
- A wholly UK owned company able to provide whichever waste recycling equipment is the absolute best for each customer's needs. No one dictates to us which machinery we must offer.
- Preventative Maintenance Contracts available on all waste recycling equipment. You can keep your investment in the optimum condition by allowing us to service your machines on a regular basis. We have a range of options to assure the accuracy and efficiency of your purchase.
Waste Recycling Equipment for:
Demolition Waste
Electronics Waste
Waste from Energy
Glass Waste
Packaging Waste
Plastics Waste
Rubber & Tyre Waste
Wood Waste
Waste Management
MRFs
Summit Recycling Overview
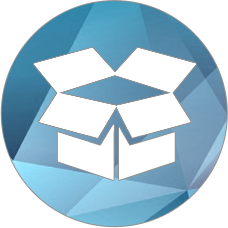
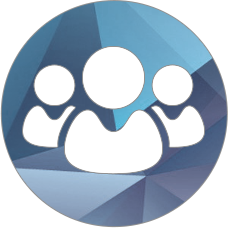
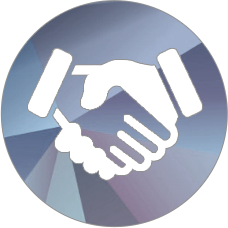