Maxmag Moulded Magnets Ltd
We manufacture magnets via injection moulding process, a method of making precision components in complex shapes with tight tolerances.
Our expertise in applied magnetics, enables us to create magnets with value added features. This versatility enables design engineers to place magnetic signals precisely, giving them more freedom when designing a complex solution.
We are able to offer sampling, small batch runs all the way through to volume production and post-operative assembly.
Due to the aggressive nature of magnetic material, good tool maintenance is key to the lifespan of the tool and quality of the components. Being able to offer this service in-house enhances the productivity of a magnet mould tool.
Anistropic magnets
Isotropic magnets have magnetic properties equal in any direction. Whilst Anisotropic magnets have a superior performance in a specified direction or pattern. The majority of our magnets are anisotropic and our unique technology enables us to maximise the magnetic strength by orientating the magnetic material during the moulding process. We can orientate the magnets axially, radially, conically or in pattern combinations.Thus giving a repeatable magnetic field each time a component is moulded
Multipole Magnets
Most of our existing customers - utilise multipole magnets and we can create poles on external or internal surfaces. Poles can be equispaced or configured specifically for a component solution.
These types of magnets are often used in drive couplings, small motors and for motion sensing using a reed switches, hall effect or inductive sensors.
We have vast experience in the design and manufacture of injection mould tooling that allows us to mould a magnet, then overmould a polymer shape around it. We are also able to insert mould onto metal spindles and bushes, or existing plastic components, giving enhanced value added solutions.
Anisotropic magnets have a superior performance in some preferred direction or pattern. They are usually three to four times as strong magnetically as isotropic magnets.
Magnetic Materials
Also Maxmag has developed a range of materials providing a variety of magnetic strengths and physical properties. Consisting of magnetic micro-powders bonded in a polymer matrix, they are designed to maximise specific properties for diverse applications.
By recommending the correct polymer we are able to offer solutions for mechanical strength, high electrical resistance and a range of working temperatures.
We also manufacture and supply our own Ferrite filled Polypropylene, that has been approved by WRAS for cold water contact
Magnet tool manufacture
Being in the same production facility, the in-house toolroom gives Maxmag a competitive advantage over other suppliers, reducing leadtimes and downtimes on production and maintenance.
We offer a proactive approach to project management, from component design through to tool manufacture, sampling and volume production.
Due to the aggressive nature of the magnetic material, good tool maintenance is key to the lifespan of the tool and quality of the components. Being able to offer this service in-house enhances the productivity of a magnet mould tool.
Magnet sectors
We have gained an enviable knowledge and wealth of experience of complex insert and overmoulding processes. This experience has ensured that we have the capability to incorporate flexibility into the design of the injection moulding tool, enabling us to accommodate the wider tolerances of metal parts, that are then overmoulded.
Our experience with the insert and overmoulding processes has put us at the forefront of the current trend to replace metal with plastic components. Working closely with our suppliers and customers we have provided intelligently engineered solutions utilising the overmoulding process. Incorporating both metal and plastics to give a value added solution, whilst maintaining the integrity and stability that a normal metal component would provide
Ferrite Magnets
Our magnets are manufactured from Ferrite filled Polymers, such as Nylon 6, Ferrite filled nylon 12, Ferrite Filled Polypro. We have our own Ferrite Fille Polypropylene material that is approved by WRAS for cold water use.
Injection moulding a Ferrite magnet leaves out the inherent brittleness of a sintered Ferrite magnet and means that you can make more complex shapes in magnetic material.
Permanent Magnets
Our Magnets are manufactured utilising the injection moulding process, we are the only UK manufacturer who makes magnets in this way. This means that a fully magnetised component is produced in one process saving post processes of moulding a component, moving into a fixture and then magnetising it by applying a current.
Our injection moulded magnet process means that each magnet is the same, each time ones comes off the press. Giving good tolerances and repeatability.
Injection moulded Ferrite Magnets
Our expertise in applied magnetics, enables us to injection mould fully magnetised components within the moulding cycle time. This versatility enables design engineers to place magnetic signals precisely, between the interface of mechanical and electronic systems, giving them more freedom when designing a complex solution.Magnets can be made into impellors, gear teeth and as they are polymer based, they have a similar versatility to a plastic component with a magnet glued in, but usually with less cost.
A precision magnet can replace a sub assembly.
We can mouldgearteeth, thread forms, spindles, rib slots, cams and cross holes as part of the magnet
We can overmould and assemble magnets onto plastic bushes, metal spindles and other threaded inserts
Less need for post assembly
Less need for post operative machining
Maxmag Moulded Magnets Ltd Overview
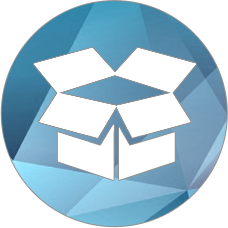
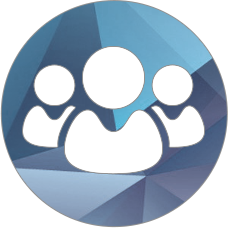
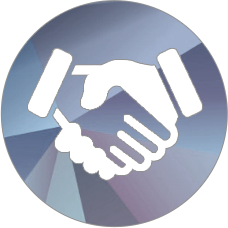